Das Zementwerk der HeidelbergCement AG in Triefenstein-Lengfurt arbeitet dank einer neuen Druckluftstation mit vier GA-Schraubenkompressoren von Atlas Copco erheblich effizienter. Der Hauptgrund für die Neugestaltung war die Modernisierung und Ausweitung der Produktionsanlagen.
Seit März 2015 speist nun ein drehzahlgeregelter Schraubenkompressor GA 90 VSD von Atlas Copco die Druckluft gemeinsam mit drei weiteren GA-90-Kompressoren in das 6,5-bar-Netz des Werkes ein. Das optimale Zusammenspiel aller Kompressoren regelt eine übergeordnete Steuerung. Die installierte Leistung genügt heute für einen Volumenstrom von 65 Kubikmetern pro Minute. Im Regelfall laufen für die Grundlast zwei der GA-90-Kompressoren sowie die drehzahlgeregelte Maschine. Mit der neuen Anlage konnte HeidelbergCement den Leerlaufanteil erheblich reduzieren und spart pro Jahr rund 150.000 Kilowattstunden Strom.
Die zweite Kostenschraube ist der Netzdruck. Der ist zurzeit mit 6,5 bar zwar noch genauso hoch wie vor der Modernisierung, soll aber künftig nach unten optimiert werden. Da vor kurzem neue Maschinen in Betrieb genommen wurden, wartet man bei HeidelbergCement zunächst ab, ob alle Anlagen störungsfrei laufen. Wenn dies der Fall ist, soll der Druck in 0,1-bar-Schritten gesenkt werden.
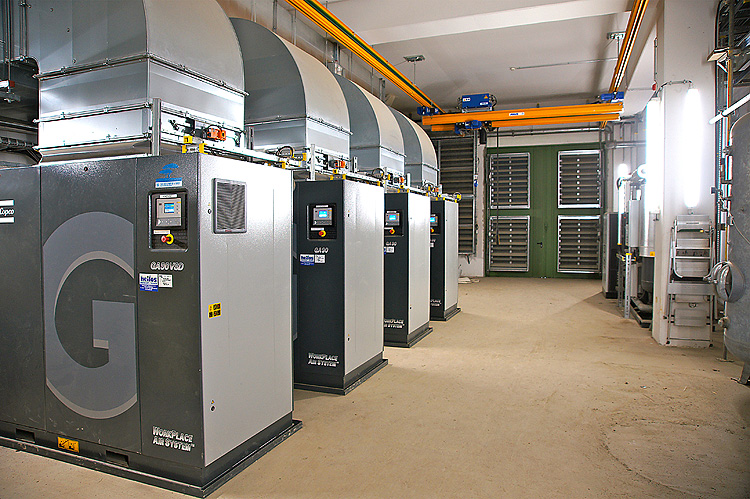
Die neue Druckluftstation wurde im März 2015 in Betrieb genommen. Ein drehzahlgeregelter Schraubenkompressor GA 90 VSD von Atlas Copco speist die Druckluft gemeinsam mit drei weiteren GA-90-Kompressoren in das 6,5-bar-Netz des Werkes ein.
Bereits heute profitiert das Werk von den Einsparungen durch eine jahreszeitabhängige Strategie zur Druckluftaufbereitung. So durchläuft die Druckluft in den Sommermonaten einen Aktivkohle- und einen Feinstaubfilter sowie einen Kältetrockner, bevor sie mit der gewünschten Qualität und dem erforderlichen Taupunkt ins Netz gelangt. In der kalten Jahreszeit wird der Kältetrockner durch einen energieintensiveren Adsorptionstrockner ersetzt, der einen geringeren Taupunkt sicherstellen kann. „Das jahreszeitabhängige Aufbereitungskonzept lohnt sich hier aufgrund der Größenordnung des Luftbedarfs absolut“, erklärt Jörn-Olaf Schröder, Technischer Berater bei Atlas Copco. „Mit dem Kältetrockner kann das Werk in der warmen Jahreszeit energetisch noch einmal richtig sparen.“
Eine weitere Schraube im Effizienzkonzept des Unternehmens soll künftig die Abwärmenutzung aus den Kompressoren sein. Alle Kompressoren im Unternehmen verfügen über eine integrierte Wärmerückgewinnung. Mit der Abwärme wird demnächst die Heizung im Labor- und Leitstandgebäude unterstützt. Damit spart das Unternehmen rund 50.000 Liter Heizöl pro Jahr.
Das meint unser Kunde:
Dominik Azadi, Leiter der Instandhaltung und verantwortlich für das Energiemanagementsystem im Zementwerk Lengfurt der HeidelbergCement AG:
„Betriebswirtschaftlich haben wir nun den großen Vorteil, dass wir mit der neuen Anlage den Leerlaufanteil erheblich reduzieren konnten. Auf diese Weise sparen wir pro Jahr rund 150.000 Kilowattstunden Strom ein.“
Das senkt den Energiebedarf:
• Drehzahlregelung
• Übergeordnete Steuerung
• Jahreszeitabhängige Druckluftaufbereitung
Die Vorteile auf einen Blick:
• Sichere Druckluftversorgung
• Deutliche Effizienzsteigerung
• Module zur Wärmerückgewinnung bereits ab Werk in die Kompressoren integriert
Ihr Ansprechpartner:Helmut Bacht, Tel. 0201/2177-522
12/2016