Der Generika-Hersteller Salutas hat in seinem Werk in Barleben die Druckluftversorgung komplett saniert. Die Versorgungssicherheit stieg, die Energieeffizienz wurde verbessert. Qualitativ entspricht die erzeugte Druckluft den strengen Normen der Pharma-Branche und erfüllt sogar die hohen Standards des US-Marktes.
„Die Salutas Pharma GmbH in Barleben zählt zu den modernsten Pharmaproduktions- und Logistikzentren Europas“, erklärt Projektingenieur Christian Dörge, der unter anderem für die Druckluftversorgung des Generika-Herstellers verantwortlich ist. An die Druckluft gibt es in Barleben zwei Anforderungen: Zum einen muss die Versorgung absolut sicher sein, da mit einer Störung Produktionsausfälle in immenser Höhe verbunden wären. Zum anderen muss die Qualität der Druckluft jederzeit den hohen Anforderungen der Pharmaindustrie entsprechen. „Wir arbeiten hier gemäß der ISO 8573.1 mit einem Restpartikel- und Restölgehalt entsprechend Klasse 1 und einer Restfeuchte entsprechend Klasse 2, das heißt mit einem Taupunkt von minus 40 Grad Celsius“, beschreibt Dörge die Qualitätsvorgaben.
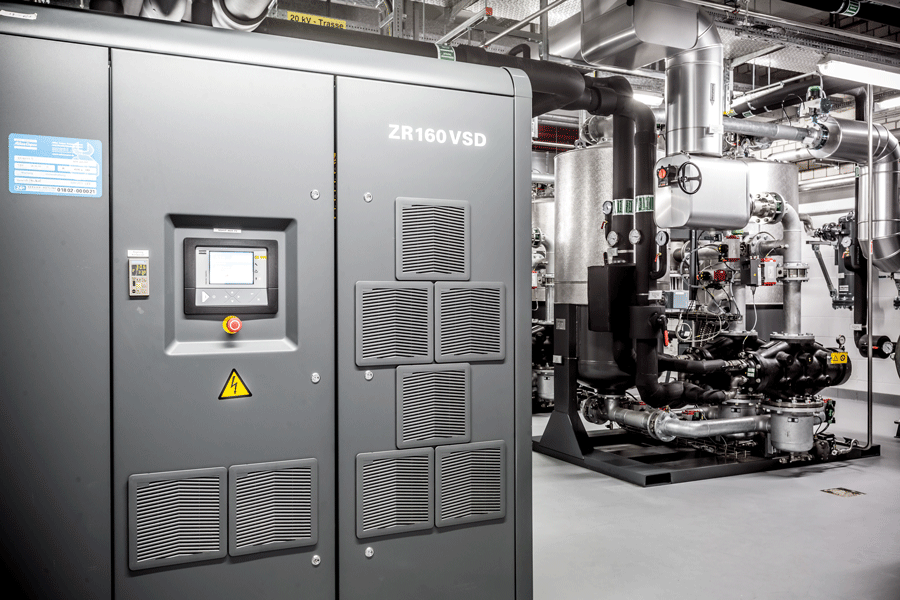
Atlas Copco errichtete für Salutas zwei neue Druckluftstationen mit insgesamt sechs Kompressoren. Das Konzept erfüllt nicht nur die Anforderungen an die Versorgungssicherheit und Druckluftqualität, sondern verbessert die Effizienz durch den Einsatz drehzahlgeregelter Kompressoren und die „Heat-of-Compression“-Technologie.
Mit den beiden im Herbst 2015 komplett erneuerten Druckluftstationen, die in ein gemeinsames Netz einspeisen, lassen sich die geforderten Werte sicher einhalten. In der Station BT 3.0 arbeiten vier ölfrei verdichtende Schraubenkompressoren von Atlas Copco: ein drehzahlgeregelter ZR 160 VSD sowie zwei ZR 160 und ein ZR 200 mit konstanten Drehzahlen. Die beiden Kompressoren in der kleineren Station BT 8.2 sind ebenfalls ölfrei verdichtende „Schrauben“: ein drehzahlgeregelter ZT 160 VSD und ein ZT 145 mit konstanter Drehzahl. Diese teilen sich den Platz mit zwei warmregenerierenden Adsorptionstrocknern BD 850+ ZP mit Erhitzer und externem Gebläse sowie mit zwei Sätzen Druckluftfiltern.
In der BT 3.0 erzeugen drei warmregenerierende Adsorptionstrockner des Typs XD 850+ G ZP zusammen mit drei Filtersätzen die erforderliche Druckluftqualität. Dabei wird das sogenannte „Heat-of-Compression“-(HOC-)Verfahren in besonderer Form eingesetzt. Die ZR-Kompressoren für diese Station wurden als Heißluftvariante (ohne Nachkühler) geliefert und stellen die für den Regenerationsprozess der Adsorptionstrockner erforderliche Heißluft bereit. „Die globalen Vorgaben unserer Konzernmutter Novartis empfehlen das „Heat-of-Compression“-Verfahren für die Regeneration des Trockenmittels“, erklärt Dörge. „Wir können dadurch im Vergleich zu früher rund 180 Kilowatt Kompressorleistung einsparen.“
Eine übergeordnete ES-16-Steuerung von Atlas Copco organisiert das Zusammenspiel der sechs Kompressoren und überträgt zudem alle Daten der angeschlossenen Kompressoren, Trockner und Filter an das Leitsystem. Normalerweise übernehmen in der großen Station zwei bis drei Kompressoren zusammen mit ein bis zwei Trocknern die Druckluftversorgung; in der kleinen Station sind dann zusätzlich ein Kompressor und ein Trockner in Betrieb. In den Stationen kann zudem jeder Kompressor mit jedem Trockner zusammenarbeiten. Eine lastabhängige Klappensteuerung stellt dabei sicher, dass nur so viele Trockner arbeiten, wie für die aktuelle Drucklufterzeugung in der Station benötigt werden. Darüber hinaus verfügen die Trockner in beiden Stationen über eine sogenannte taupunktabhängige Abschaltung bei unzureichendem Drucktaupunkt. Pro Station werden jeweils ein Kompressor und ein Trockner als Redundanz vorgehalten. Außerdem ergänzen sich beide Stationen im Falle einer Störung.
Mit diesem Konzept sieht Christian Dörge seine Anforderungen an die Druckluftversorgung durchgehend erfüllt. Zum einen rechnet der Projektingenieur mit erheblichen Energieeinsparungen. Zum anderen sieht Dörge den Standort auf Jahre hinaus gut aufgestellt: „Wir haben hier nicht nur bezüglich der lieferbaren Druckluftmenge, sondern auch der Qualität in die Zukunft investiert; denn die Standards in der Pharmazie werden über die Zeit eher höher als niedriger sein.“
Die Vorteile auf einen Blick
►Sehr hohe Versorgungssicherheit
►Qualitätsanforderungen an die Druckluft werden jederzeit sicher erfüllt
►Energie- und Kosteneinsparungen durch den Einsatz des „Heat-of-Compression“-(HOC-)Verfahrens
Ihr Ansprechpartner:Ulrich Ostermann, Tel. 0201/2177-439
März 2017