Wenn Sie ein Druckluftsystem haben, das mehr als einen Kompressor oder Trockner verwendet, kann es schwierig sein, zu bestimmen, welche Maschine wann laufen soll. Dies gilt insbesondere, wenn Ihr Bedarf täglich schwankt. Wenn Ihr System nicht richtig gesteuert wird, besteht die Gefahr, dass Sie zu viel Luft produzieren, was wiederum zu hohen Energiekosten führt. Die Lösung: eine übergeordnete Kompressorsteuerung.
Was ist eine übergeordnete Kompressor-Steuerung?
Je nach Hersteller gibt es unterschiedliche Arten übergeordneter Steuerungssysteme. Bei Atlas Copco haben wir vor kurzem eine neue Generation zentraler Kompressor Steuerungen vorgestellt – den Optimizer 4.0. Der Regler wählt die effizienteste Kombination von definierten Arbeitsdrücken aus und gleicht die Betriebsstunden der Einheiten aus, um eine ungleiche Abnutzung der Kompressoren zu verhindern und die Wartungsintervalle zu minimieren. Über die intuitiv zu bedienende Benutzeroberfläche kann der Anwender bzw. die Anwenderin auf die Leistungsdaten und den Energieverbrauch jeder einzelnen Maschine zugreifen und erhält einen Einblick in die Leistung des gesamten Systems.
Was unterscheidet den Optimizer 4.0 von anderen Kompressor-Steuerungen?
Der Name unserer neuesten fortschrittlichen Steuereinheit ist Programm. Der Optimizer der neusten Generation steuert bis zu 30 Kompressoren und 30 Trockner über Can-Bus – um die Maschineneffizienz und -auslastung Ihrer Druckluftanlage zu maximieren. Der Kompressor kann nach Volumenstrom ausgewählt und nach Druck geregelt werden. Das vermeidet Leerlauf-Zeiten und senkt gleichzeitig die Lebenszykluskosten. An dieser Stelle sei gesagt, dass durch den Optimizer 4.0 nicht nur die Energiekosten gesenkt, sondern auch die Verfügbarkeit und Zuverlässigkeit von Druckluftstationen erhöht werden.
Neben Atlas Copco Kompressoren (lastleerlauf- und drehzahlgeregelte Kompressoren) können auch Kompressoren anderer Hersteller über Schnittstellenmodule integriert werden. Darüber hinaus ist der Optimizer auch in der Lage, drei verschiedene Druckluftnetze gleichzeitig zu steuern, was Ihn zu einer sinnvollen Investition macht.
Wieso es sinnvoll ist eine übergeordnete Kompressor-Steuerung einzusetzen
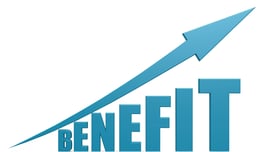
Nachfolgend finden Sie sechs Gründe, warum Ihr Druckluftsystem von einer zentralen Kompressor-Steuerung profitieren kann.
- Flexible Maschinensteuerung - Steuerungen sorgen dafür, dass die Maschinen in Gruppen arbeiten und sich an den Bedarf anpassen. In einem festen System gibt es möglicherweise eine bestimmte Reihenfolge, in der die Maschinen eingesetzt werden, um den Luftbedarf zu decken. In einem flexiblen System mit einer Kompressor-Steuerung wird die beste Kombination von Maschinen eingesetzt. So ist eine optimale Versorgung Ihrer Produktion gewährleistet.
- Ausgleich der Arbeitslast - Durch die Verteilung der Arbeitslast auf mehrere Maschinen vermeidet eine zentrale Steuerung eine unnötige Überlastung einzelner Maschinen. Eine Kompressor-Steuerung kann auch den Einsatz der wirtschaftlichsten Maschinen gegenüber älteren, weniger effektiven Versionen priorisieren.
- Kontinuierlicher Einsatz von VSD-Maschinen - VSD-Kompressoren sind die energieeffizientesten Maschinen für variable Last. Eine zentrale Steuerung kann sicherstellen, dass diese Maschinen Vorrang vor Grundlast- oder einstufigen Kompressoren haben.
- Regelung des Systemdrucks - Mit einer zentralen Steuerung können die Maschinen innerhalb eines vordefinierten und engen Druckbandes betrieben werden. So kann das System den Bedarf decken und gleichzeitig die Energieeffizienz optimieren.
- Abschaltplanung - Zentrale Kompressorsteuerungen können Betreiber:innen helfen, Wartungsarbeiten zu planen und zusätzliche Kosten während der arbeitsfreien Zeit zu vermeiden. Geplante Abschaltungen sollten Teil eines jeden vorausschauenden Wartungsplans sein.
- Weniger Serviceeinsätze - Durch die flexible Sequenzierung der Maschinen, den Ausgleich der Arbeitslast und die Planung von Abschaltungen helfen die zentralen Kompressorsteuerungen den Maschinen, vorzeitigen Verschleiß zu vermeiden. Dies führt zu weniger Serviceeinsätzen und damit zu niedrigeren Service- und Wartungskosten.
So haben Sie Ihre Kompressordaten jederzeit verfügbar
Neu im Programm ist der Equalizer 4.0 Pro. Lesen Sie jetzt, was ihn vom Vorgängermodell unterscheidet, und weshalb er für alle Druckluftstationen mit mehreren Kompressoren und Druckluftaufbereitung geeignet ist.
Der Equalizer 4.0 Pro ist eine Erweiterung des Vorgängers „Equalizer“, denn er verbindet nicht nur Kompressoren untereinander, sondern zugleich auch Trockner. Dabei können ab sofort bis zu acht Kompressoren miteinander verbunden werden und miteinander kommunizieren. Außerdem ist ein Upgrate zum Optimizer 4.0 jederzeit möglich.
Von den angeschlossenen Kompressoren stehen alle Maschinendaten zum Abruf über den kapazitiven 12” Bildschirm zur Verfügung. Eine Datenanalyse und Visualisierung der Kompressorstation kann per Knopfdruck am Bildschirm erfolgen.
Über den Bildschirm der Kompressorsteuerung sind folgende Information abrufbar:
- Informationen zum Druckluftnetz & den Kompressoren
- Ereignis-Historie
- Trend-Grafen
- Serviceinformationen
Durch den Remote Fernzugriff können durch einfaches Duplizieren des Displays alle Informationen am PC abgerufen werden. Durch Nutzung der IP-Adresse des UNO-PC kann von allen im kundenseitigen Netzwerk integrierten PC auf die Equalizer PRO-Steuerung zugegriffen werden.
Das könnte Sie auch interessieren:
▶ Lesen Sie in unserem Druckluft-Wiki mehr über zentrale Steuerungssysteme in Druckluftanlagen
▶ Atlas Copco - übergeordnete Steuerungen für Kompressoren