Containerlösung stellt mit öleingespritzten Schraubenkompressoren qualitativ hochwertige Druckluftversorgung sicher.
Eine übergeordnete Steuerung von Kompressoranlagen sorgt für wenig Leerlaufzeiten, optimale Auslastung, bedarfsgerechte Erzeugung der Druckluft, Senkung der Energiekosten und somit zu höchster Effizienz. Zudem bietet die Unterbringung in den Containern Sicherheit vor Staub und Lärmemissionen.
🎧Artikel als Podcast anhören, Dauer 3:23 Min🎧
Druckluftversorgung zur Herstellung von Gipskartonplatten
Daraus entstand über die Jahre ein dezentrales Druckluftkonzept in Form von drei Insellösungen, die sich bei Störungen nicht gegenseitig unterstützen konnten. Der Ausfall eines Kompressors gab den Anlass, das Gesamtkonzept unter die Lupe zu nehmen und nach Verbesserungspotenzialen abzuklopfen. Diese Aufgabe übernahm die Wiewald GmbH, Leipzig, ein langjähriger Partner der Lippendorfer und Atlas-Copco-Vertragshändler.
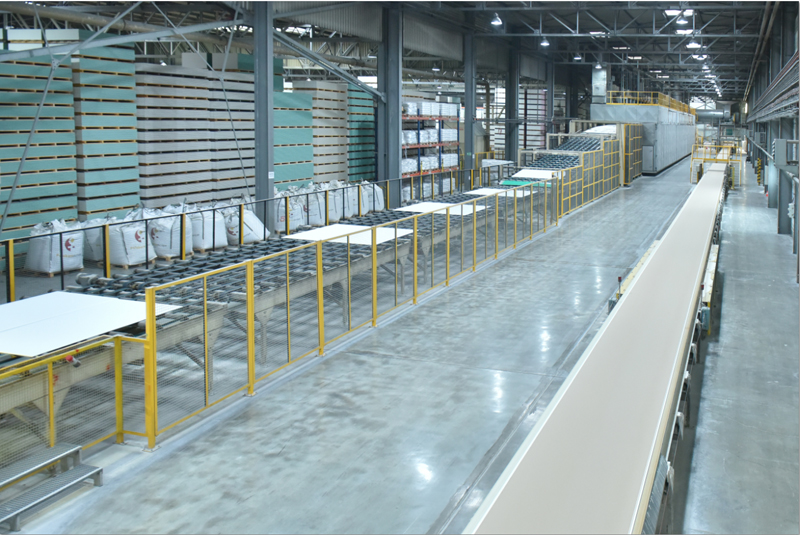
Aufgrund der Staubbelastung in der Werkshalle war man sich schnell einig, dass die neue Station in einem Container außerhalb des Gebäudes untergebracht werden sollte. „Für den Container haben wir ein maßgeschneidertes Konzept entwickelt“, berichtet Ilja Koschew, Meister Instandhaltung bei EBP. „Das begann mit der Auswahl des Aufstellungsortes, dem Einsetzen der Türen und der Innenisolierung.“ Darüber hinaus habe man sich im Vorfeld viele Gedanken über die Sensorik und Steuerung gemacht, um später im Betrieb nicht dauernd selber eingreifen zu müssen.
Das sagt unser Kunde:
„Wir sind davon ausgegangen, dass wir durch die neue Anlage 35.000 Euro pro Jahr einsparen. Das hat sich auch bewahrheitet.“
Jörg Langrock, Werkleiter bei der Etex Building Performance GmbH
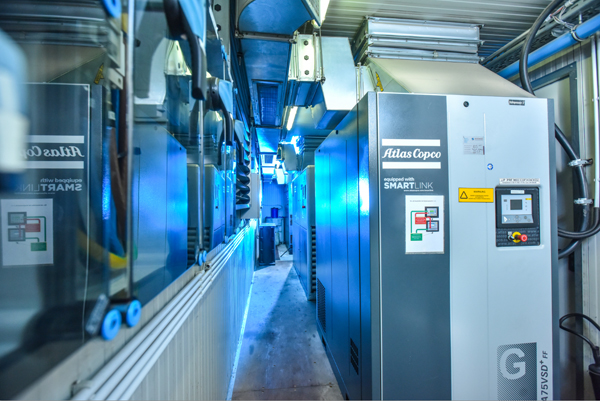
Industriekompressoren platzsparend und sicher im Container
Wie die übergeordnete Steuerung Leerlaufzeiten der Druckluftanlage auf ein Minimum beschränkt
Alle Kompressoren sowie die Aufbereitungstechnik und verschiedene Sensoren werden von einer übergeordneten Steuerung so dirigiert, dass sie reibungslos und möglichst effizient zusammenarbeiten. „Mit den verschiedenen Kompressoren können wir heute jeden Bedarf im Unternehmen abbilden“, hebt Koschew hervor.
"Früher haben wir unnötig viel Druckluft produziert. Damals lag das Last-Leerlauf-Verhältnis bei 50 zu 50. Heute haben wir den Leerlaufanteil durch die drehzahlgeregelten Maschinen und die Steuerung auf ein Minimum gesenkt.“
>>Erfahren Sie mehr zu übergeordneten Steuerungen
>>Energiesparen in Fertigungsbetrieben:
Welche Ansatzpunkte der Kompressor bietet
Bedarfsgerechte Drucklufterzeugung senkt Energiekosten
Die bedarfsgerechte Erzeugung hat die Energiekosten für die Druckluft deutlich reduziert. „Wir sind davon ausgegangen, dass wir durch die neue Anlage 35.000 Euro pro Jahr einsparen. Das hat sich auch bewahrheitet“, bilanziert EBP-Werkleiter Jörg Langrock. „2016 hatten wir hier ungefähr 146.000 Euro an Energiekosten für die Druckluft bei einem Verbrauch von rund einer Million Kilowattstunden. Mit der Installation der neuen Anlage sind die Kosten 2017 auf rund 111.000 Euro gesunken.“ Durch weitere Optimierungen erwartete man für die Folgejahre sogar noch größere Einsparungen.
Darüber hinaus ist die Drucklufterzeugung aufgrund der Steuerung heute deutlich transparenter. Daten zu produzierter Druckluftmenge und Energieverbrauch sind kontinuierlich verfügbar. Störungen werden direkt gemeldet und können häufig selbst behoben werden. Ein angepasster Wartungsvertrag mit Wiewald in Verbindung mit dem internetbasierten Datenüberwachungsservice Smartlink von Atlas Copco ermöglicht zudem eine proaktive Instandhaltungsstrategie.
Sind Sie an weiteren Anwenderberichten unserer Druckluftkunden interessiert, dann lesen Sie auch folgende Artikel:
-
Anwenderbericht Maschinenbau: Kaum Blindstromkosten dank drehzahlgereglter Industriekompressoren
-
Wie eine Wertstoffsortieranlage Druckluft aus dem Container einsetzt
-
Podcast: Ohne Druckluft kein Eis! Wie eine effiziente Druckluftstation für mehr Eis sorgt.
-
Perfekt für Abwasseraufbereitung & pneumatische Förderung: Turbogebläse für Überdruck bis 1,4 bar
-
Anwendervideo: Schädlingsbekämpfung mit CO2 in der Lebensmittelverarbeitung
-
Entscheidungshilfen für das Be-/Entladen von Silos mit Niederdruck-Gebläsen